Mastering the Art of Welding: How to Avoid Undercut Welding Issues for Flawless Construction Outcomes
By understanding the root causes of undercut welding and implementing effective methods to avoid it, welders can raise their craft to brand-new degrees of excellence. In the pursuit of flawless construction results, grasping the art of welding to stay clear of undercut problems is not just a skill however a requirement for those making every effort for excellence in their job.
Recognizing Undercut Welding
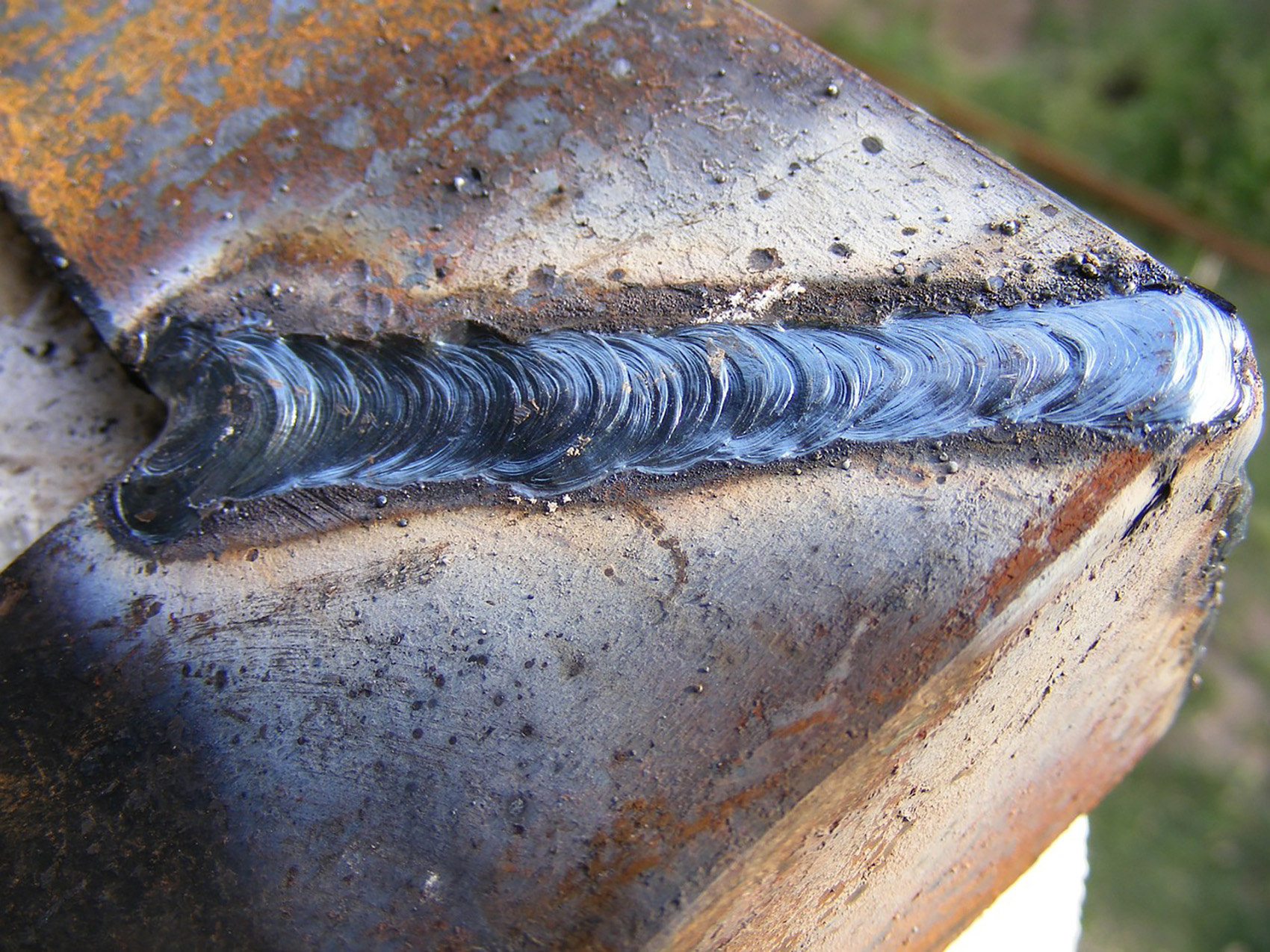
To prevent undercut welding, welders need to ensure proper welding specifications, such as changing the present, voltage, travel rate, and maintaining the correct electrode angle. By understanding the causes of undercut welding and implementing preventive procedures, welders can attain high-quality, structurally audio welds.
Reasons of Undercut in Welding
Comprehending the factors that contribute to damage in welding is vital for welders to generate top quality, structurally audio welds. Inadequate welding incorrect or present welding rate can also add to damage. Understanding these causes and applying proper welding techniques can assist stop damaging issues, ensuring solid and sturdy welds.
Methods to stop Undercutting

To minimize the danger of undercutting in welding, welders can use tactical welding techniques aimed at enhancing the quality and honesty of the weld joints. In addition, utilizing the appropriate welding technique for the details joint setup, such as weave or stringer beads, can add to minimizing undercutting.
Employing back-step welding strategies and controlling the weld grain profile can likewise aid distribute warmth equally and reduce the threat of undercut. Regular assessment of the weld joint throughout and after welding, as well as executing quality guarantee measures, can help in resolving and identifying undercutting concerns promptly.
Significance of Correct Welding Parameters
Selecting and additional reading maintaining suitable welding specifications is essential for achieving successful welds with very little issues. Welding parameters describe variables such as voltage, current, travel speed, electrode angle, and protecting gas flow price that straight influence the welding procedure. These criteria must be carefully changed based on the kind of product being bonded, its density, and the welding strategy utilized.
Appropriate welding specifications make certain the correct amount of warmth is applied to melt the base steels and filler product evenly. If the criteria are established too expensive, it can cause extreme warm input, triggering distortion, spatter, or burn-through. On the other hand, if the specifications are too her comment is here low, insufficient blend, absence of penetration, or damaging might take place.
Quality Control in Welding Workflow
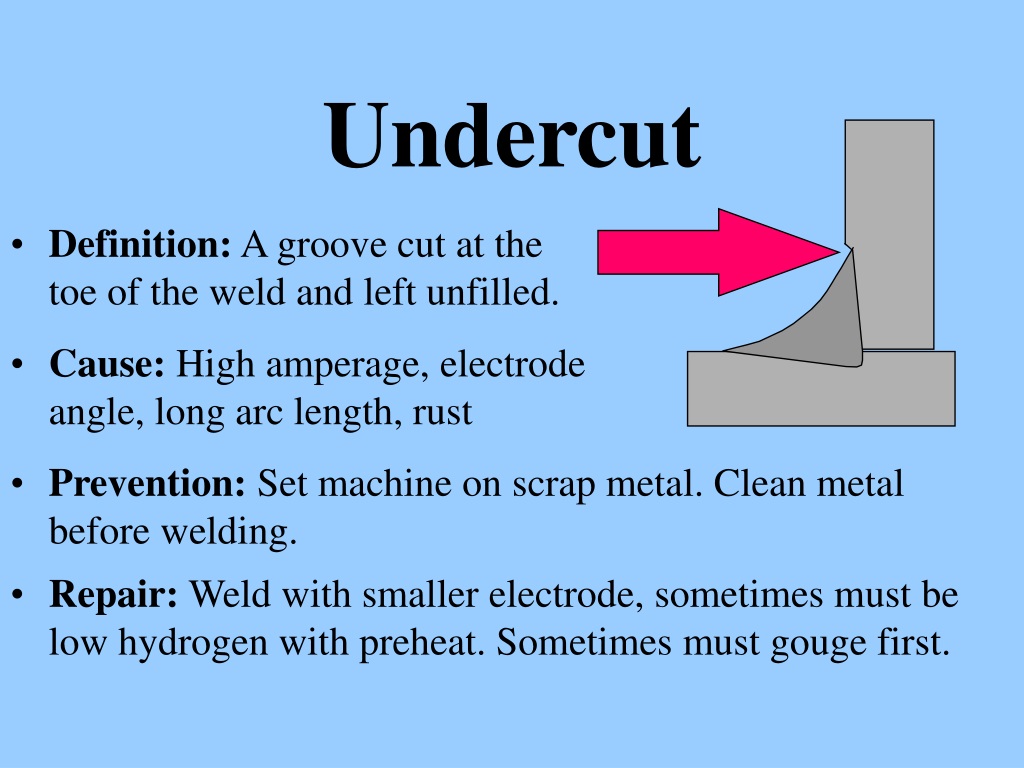
Verdict
Finally, grasping the art of welding requires a thorough understanding of undercut welding, its reasons, and techniques to stop it. By making certain proper welding criteria and carrying out quality control practices, remarkable construction outcomes can be accomplished. It is important for welders to continually aim for quality in their welding operations to stay clear of undercut problems and generate premium welds.
Undercut welding, a common flaw in welding procedures, takes place when the weld steel does not effectively fill up the groove and leaves a groove or anxiety along the welded look what i found joint.To avoid undercut welding, welders must ensure proper welding specifications, such as changing the current, voltage, travel rate, and maintaining the right electrode angle. Inadequate welding present or inaccurate welding rate can additionally contribute to damage.To minimize the threat of undercutting in welding, welders can use calculated welding strategies aimed at boosting the high quality and stability of the weld joints.In conclusion, grasping the art of welding calls for an extensive understanding of undercut welding, its reasons, and strategies to prevent it.
Comments on “Ultimate Overview to Preventing Weld Undercut: Tips and Techniques”